A Guide To RF Welding For Medical Device Manufacturing
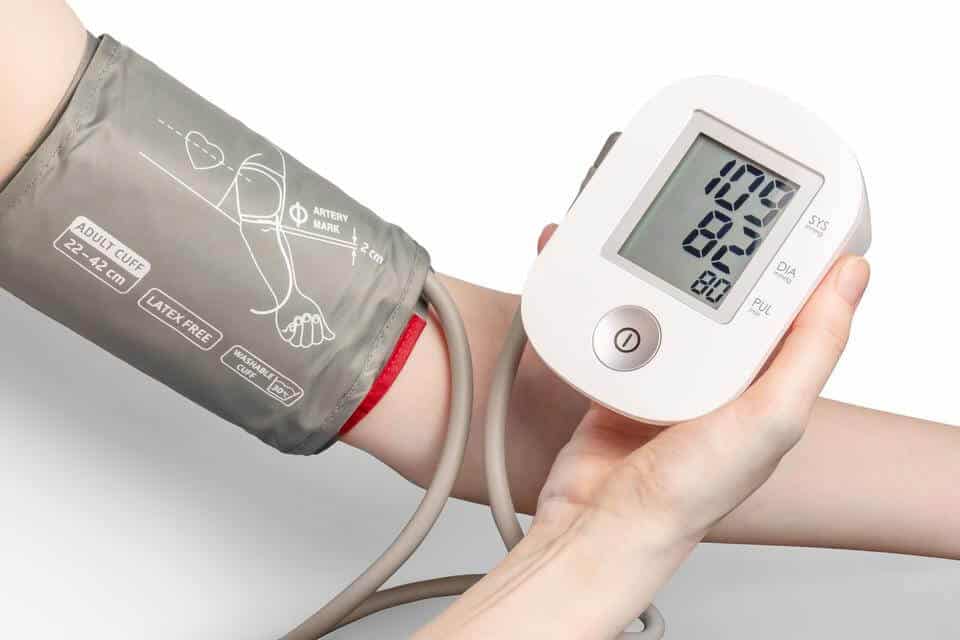
For many years, medical RF welding has been used in the device manufacturing industry for seals to make such products as bags for intravenous infusions and for the collection of bodily fluids.
As the industry has grown rapidly with the aging of the population, the demand for more disposable bags and other PPE has grown by leaps and bounds. Most PPE used every day in hospitals across the world is made with this technology.
What is Medical RF Welding?
Also known as radiofrequency welding, medical RF welding is a specialized technique used in the medical industry to join or seal thermoplastic materials together. It involves the application of high-frequency electromagnetic energy to heat and melt the surfaces of the materials, creating a strong bond when they cool and solidify. This process is commonly used for manufacturing medical devices such as bags, pouches, tubing, and inflatable products, where a reliable and secure seal is crucial to maintain the integrity of the contents or to prevent contamination.
You can always learn more about RF welding and dielectric welding of medical plastics in this article from ScienceDirect.
What Are the Benefits of Medical RF Welding?
Medical RF welding offers several advantages, including the ability to create hermetically sealed seams without the need for adhesives or stitching, ensuring a smooth, clean surface that is resistant to fluid ingress and easy to clean. Medical RF welding’s ability to produce hermetic seals ensures medical devices remain sterile, which is critical in patient care.
This welding method is known for its consistency, reliability, and efficiency, providing high-quality seals without contamination risk. Moreover, medical RF welding enables precise control over the welding parameters, resulting in consistent and reproducible welds with minimal thermal damage to the surrounding materials.
Medical RF welding is environmentally friendly, as it does not require toxic adhesives or solvents. Its versatility across various material thicknesses further underscores its advantages, highlighting why this technology is indispensable in manufacturing medical products.
What Are Some Products Made with Medical RF Welding?
Medical RF welding is instrumental in producing a wide range of medical devices and equipment. From IV bags and blood pouches to surgical drapes and wound care products, medical RF welding ensures medical items meet the highest quality and safety standards.
Intravenous infusions, chemotherapy, blood, enteral nutrition, stoma and urology, laparoscopy, enemas, and fluid filtration bags are manufactured with medical RF welding.
In addition, this process involves blood pressure cuffs, hot compresses, cold compresses, compression leg sleeves, aerial broadcasts, body bags, wheelchair blocks, fixing pillows, breathing bags, implants, vein arm plates, stretchers, centrifuges, and sterilization.
Medical RF welding products used in manufacturing are indicators, tourniquets, catheters, liquid pump cartridges, and other disposable devices. These products are widespread and diverse, but the techniques for welding them are essentially the same.
By leveraging medical RF welding, medical device manufacturers can meet the healthcare industry’s rigorous demands, ensuring patient safety and care.
What Kinds of Materials Can’t Be Used in Medical RF Welding?
While the RF heat sealing process is extremely useful in many cases, not all plastics can go through medical RF welding and be heated at radio frequencies. Polystyrene, polypropylene, and polyethylene are common materials that do not respond to RF energy. Many medical manufacturers have invested heavily in RF systems, so there is a strong incentive to maintain RF compatibility when creating new materials, such as materials formulated in place of PVC.
How Does Medical RF Welding Compare to Other Sealing Methods?
Compared to sewing, gluing, and hot-air bonding, medical RF welding stands out for its superior performance in creating durable and reliable medical devices.
Unlike sewing, which can weaken under pressure, or gluing, which may degrade over time, medical RF welding offers a more robust solution that withstands stress and environmental factors. This method eliminates the need for consumables, reducing production costs and enhancing the biocompatibility of medical products. By offering a stronger, safer seal, medical RF welding ensures the integrity of medical devices, making it a critical process in the medical manufacturing industry.
How Does Medical RF Welding Work?
Medical RF welding is pressure-conducted through two or more layers of dielectric plastic so that when the material melts, the molecules of all plastic layers merge. When the polarity of radio waves passing through plastic changes, the polarized molecules in the polymer vibrate back and forth, causing friction at the molecular level and generating heat. This heat, when generated with sufficient energy, melts the plastic and seals the layers.
The result of this process is a seal with resistance equal to the material itself. The seals are consistent, nearly transparent, and uniform in appearance and size. The basic RF sealer consists of a radio transmitter and a pneumatic press that opens and closes the energy applicator. Transmitters are called RF generators because they generate radio frequency wave energy instead of transmitting radio signals.
When Was RF Welding First Used For Medical Devices?
The exact time when RF technology was first used for medical products is unknown, but it is estimated to be around 1945. The first types of products made with this process were items like plastic raincoats, 3-ring binders, and wallets. Subsequent overall uses of medical RF welding included medical bags, pool linings, various automotive products, tents, canopies, and packaging.
Take a look at some of the medical products that Vinyl Technology has created to see even more examples of products made with this technique.
For more information about how medical RF welding and other sealing technologies can help you meet your needs, get in touch with Vinyl Technologies today.