The Practical Applications of Poka Yoke for Error-Free Manufacturing Processes
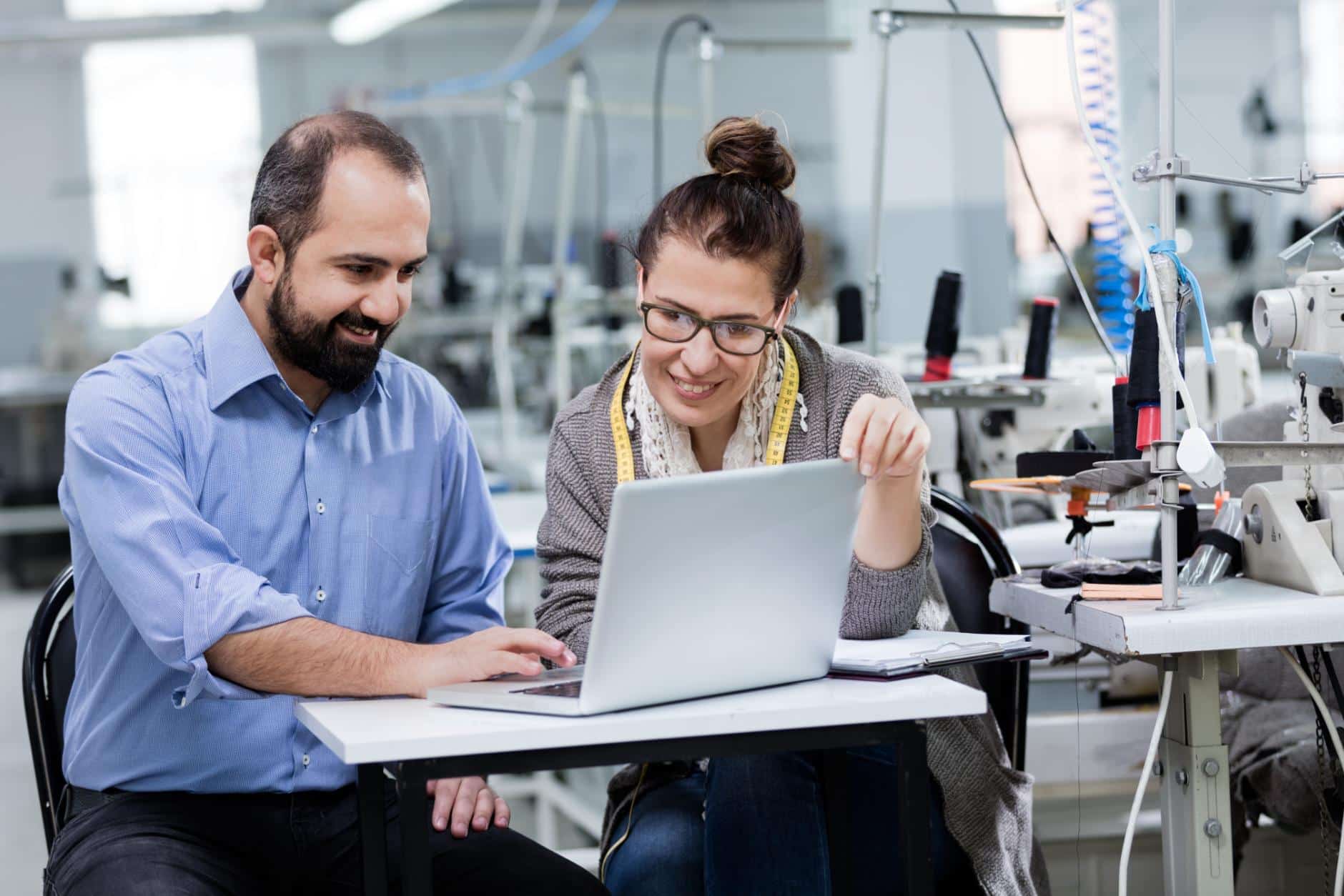
Table of Contents
- Introduction to Poka Yoke
- How Poka Yoke Prevents Mistakesa
- Examples of Poka Yoke in Manufacturing
- The Benefits of Implementing Poka Yoke
- Steps to Integrate Poka Yoke into Manufacturing Processes
- Challenges in Adopting Poka Yoke
- Vinyl Technology: Your Partner for Error-Free Manufacturing with Poka Yoke
Introduction to Poka Yoke
Poka Yoke is a process-proofing method designed to prevent errors before they occcur. The term originates from Japanese manufacturing and is often associated with lean practices. It emphasizes creating systems and tools that make mistakes nearly impossible or immediately obvious, reducing the chances of defects and improving overall efficiency.
Poka-yoke is a Japanese concept loosely adapted from the more familiar English term “idiot-proof.” Rather than assume the worker is an idiot who needs to be protected from themselves, poka-yoke instead refers to the act of avoiding a really bad move.
The primary goal of Poka Yoke is to avoid errors at their source. By integrating this philosophy into manufacturing, teams can build workflows that identify potential issues in real-time, stopping problems before they escalate. This complements lean manufacturing practices by reducing waste and improving reliability.
How Poka Yoke Prevents Mistakes
Mistakes in manufacturing processes can happen in many ways. Workers might forget a step, use the wrong material, or assemble components incorrectly. These errors can lead to defective products, wasted resources, and production delays.
Poka Yoke uses detection and prevention mechanisms to address these problems. Detection mechanisms alert workers when something is wrong, like sensors that stop a machine when parts are misaligned. Prevention mechanisms go further by designing processes that make errors impossible, like fixtures that only fit correctly assembled components or tools that won’t operate unless used properly.
The key is creating systems that are both fail-safe and user-friendly. Poka Yoke ensures that processes are designed to reduce opportunities for error while keeping workflows simple and efficient. A process that avoids mistakes at the source benefits not only production but also the workers who rely on clear, reliable systems to do their jobs well.
Examples of Poka Yoke in Manufacturing
Poka Yoke can take many forms, depending on the process’s needs. Physical devices are often used to prevent incorrect assembly. Fixtures, jigs, or guides ensure that parts fit together correctly, eliminating the possibility of misalignment.
Visual cues also play a key role. Color coding parts or processes provide workers with an easy way to identify the correct steps or materials. For example, different wire colors in electrical systems indicate where each one should connect, reducing errors during assembly.
Automated systems are another effective application of Poka Yoke. These systems can stop production when they detect an error, preventing further issues down the line. Sensors that monitor alignment or weight are common, alerting workers to problems immediately.
Real-world examples span industries like automotive, aerospace & medical device manufacturing.
In the automotive sector, connectors are designed with unique shapes to prevent incorrect installations.
In aerospace, sensors ensure precise measurements for critical components.
Medical device manufacturing uses color-coded parts and automated checks to maintain strict quality standards, protecting both patients and end-users from potential harm.
The Benefits of Implementing Poka Yoke
Poka Yoke reduces waste by minimizing defective products. Errors caught early in the process prevent wasted materials, saving time and resources that would otherwise be spent on rework or scrapped items.
Consistency in quality improves across production lines. By designing processes that eliminate the chance for mistakes, manufacturers produce uniform results. This leads to greater reliability and trust from clients who depend on consistent product performance.
Fewer errors and less downtime result in significant cost savings. Preventing mistakes reduces the need for costly corrections, while automated error-detection systems keep production lines running efficiently without unnecessary interruptions.
Worker safety also improves with error-proofing tools. Systems designed to prevent missteps can protect employees from injuries caused by mistakes, creating a safer work environment while maintaining high production standards.
Steps to Integrate Poka Yoke into Manufacturing Processes
The first step in integrating Poka Yoke is identifying common sources of errors in current workflows. This involves observing processes, gathering data, and pinpointing areas where mistakes frequently occur. Mistakes can result from human error, like skipped steps, or system defects that allow those errors to happen. Recognizing this distinction is critical to designing effective solutions.
Designing simple, low-cost solutions is the next step.
These solutions should directly address the identified errors. Vinyl Technology is not the first to apply this methodology to manufacturing — the inventor of Poka Yoke, Shigeo Shingo, created a process for assembling a small switch where workers often forgot to insert a spring under the switch buttons. Shingo broke the process into two actions:
- Preparing springs in a slot
- Inserting them into the switch from the slot
This gave workers a clear signal when the task was incomplete, eliminating errors without adding complexity.
Once solutions are designed, testing and refining them ensures reliability. Solutions must work seamlessly within the existing workflow and consistently prevent the identified errors. Iterations may be necessary to fine-tune the process and maximize effectiveness.
Training teams to recognize the value and purpose of these systems is essential for long-term success. Workers must understand how Poka Yoke helps prevent errors and why these systems make their jobs safer, more efficient, and less stressful. It was important to Shingo, just as it is important to Vinyl Technology, to address inevitable human error at its source.
This creates a safe, efficient, and cost-effective manufacturing floor, benefiting both teams and production outcomes.
Challenges in Adopting Poka Yoke
Resistance to change is a common challenge when implementing Poka Yoke. Production teams may feel skeptical about altering familiar processes, especially when they don’t immediately see the value of mistake-proofing systems. Clear communication and gradual implementation can help ease this transition.
Redesigning equipment or processes to incorporate Poka Yoke can involve upfront costs. Developing and installing error-proofing tools or adapting workflows requires an investment of time and resources. While the long-term benefits often outweigh these costs, the initial expenses can deter some manufacturers.
Continuous monitoring is required to maintain and improve these systems over time. Poka Yoke is not a one-time fix—it’s an ongoing effort to refine processes as new challenges arise. Regular evaluation ensures the solutions remain effective and adapt to changing production needs.
Vinyl Technology: Your Partner for Error-Free Manufacturing with Poka Yoke
Poka Yoke is a powerful tool for creating error-free manufacturing processes. By preventing mistakes at their source, this method reduces waste, improves quality, and enhances efficiency across production lines. Its ability to turn potential errors into opportunities for improvement makes it an essential part of modern manufacturing.
Vinyl Technology applies Poka Yoke principles to every aspect of our operations, from RF welding to custom industrial sewing. Vinyl Technology integrates poka-yoke by implementing systems for long-term learning from errors and getting input from the operators themselves.
For businesses seeking dependable manufacturing solutions, Vinyl Technology offers the expertise and commitment needed to bring Poka Yoke to life in your operations.
Submit A Project Request A Quote