What is Heat Sealing and How is It Used?
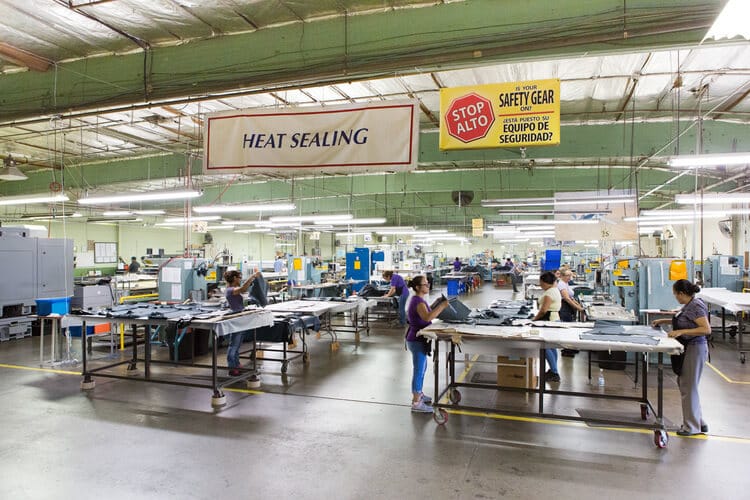
Heat sealing, also called heat welding, is a method of fastening two pieces of fabric together with an airtight, watertight bond. The most common type of heat weld uses polyvinyl chloride (PVC) or vinyl fabric. The nature of heat-sealed welding makes it perfect for lots of different kinds of thermoplastic materials, especially thinner fabrics.
Thermoplastic Materials
In order for heat sealing to work properly, the materials used must be “thermoplastic.” A thermoplastic fabric is reactive to the application of heat–it melts at a certain high temperature and becomes a liquid. This conversion from one state of matter to another is key to the process and the reason why it works so well. When two thermoplastic fabrics are melted together at the same time, the molecules of both fabrics intermingle and join together.
Common Household Uses of Heat-Seal Devices
Most of us know heat sealing from late-night TV commercials for devices that can seal familiar household items like potato chip bags. Heat sealing is perfect for this because most plastic bags used in the kitchen are thermoplastic and react extremely well to the high temperatures required. Heat seals are also good for this type of use because the bond they create, at the molecular level, is waterproof and airtight–exactly what you need for food safety and preservation.
Heat-Sealed Industrial Uses
If you guessed that heat sealing would be useful in other areas, you’d be right. The advantages of heat seals, like fire-retardant properties, oil and chemical resistance, and high durability and strength, make it the ideal solution for many industrial-strength applications. You can read about some of them on the Vinyl Technology website, like the DPE (Demilitarization Protective Ensemble), G-suits, and most medical-grade PPE.
Two kinds of heat-sealed welding apply to both the kind you’d use at home and those used by companies like Vinyl Technology: impulse and constant heat.
Impulse Thermal Sealing
Impulse sealing refers to the on-demand nature of this particular bonding process–this method is mostly used in those household applications you likely already know. The machines that produce these seals only heat up for the exact amount of time it takes to make the bond and then rapidly cools. This method uses less power than other methods and is best used for thinner fabrics that also tend to have a lower melting point.
Constant or Direct Thermal Sealing
Constant, or direct heat sealing is just what it sounds like. It typically uses two opposing elements, like metal bars, that are constantly supplied with power. This means that they’re also constantly hot, in order to maintain the higher average temperature required to make the required bonds. This method is the preferred heat seal for thick fabrics like Mylar, because of the high heat it uses.
RF Welding
Although not technically a variety of heat sealing like the kind created by impulse or constant heat sealing machines, RF Sealing, or dielectric sealing, is usually included in the menu of services provided by companies like VTI. This process uses RF waves to excite the molecules of the materials to be joined from the inside out, fusing the materials together.
When used by Vinyl Technology, RF energy is directed through electrodes (dies) custom-designed to the required shape of the seal or bond. This makes RF sealing the most versatile of the polymer film sealing methods.
Vinyl Technology also utilizes RF welding to create other products, such as chair cushions, water storage bags, and self-inflating field mattresses.
Which version of heat sealing is right for your project, and what kind of thermal seal do you need? You can get the answers to these questions and more when you get in touch with us.