RF Sealing at the Forefront of Advancing Medical Welding and Device Manufacturing
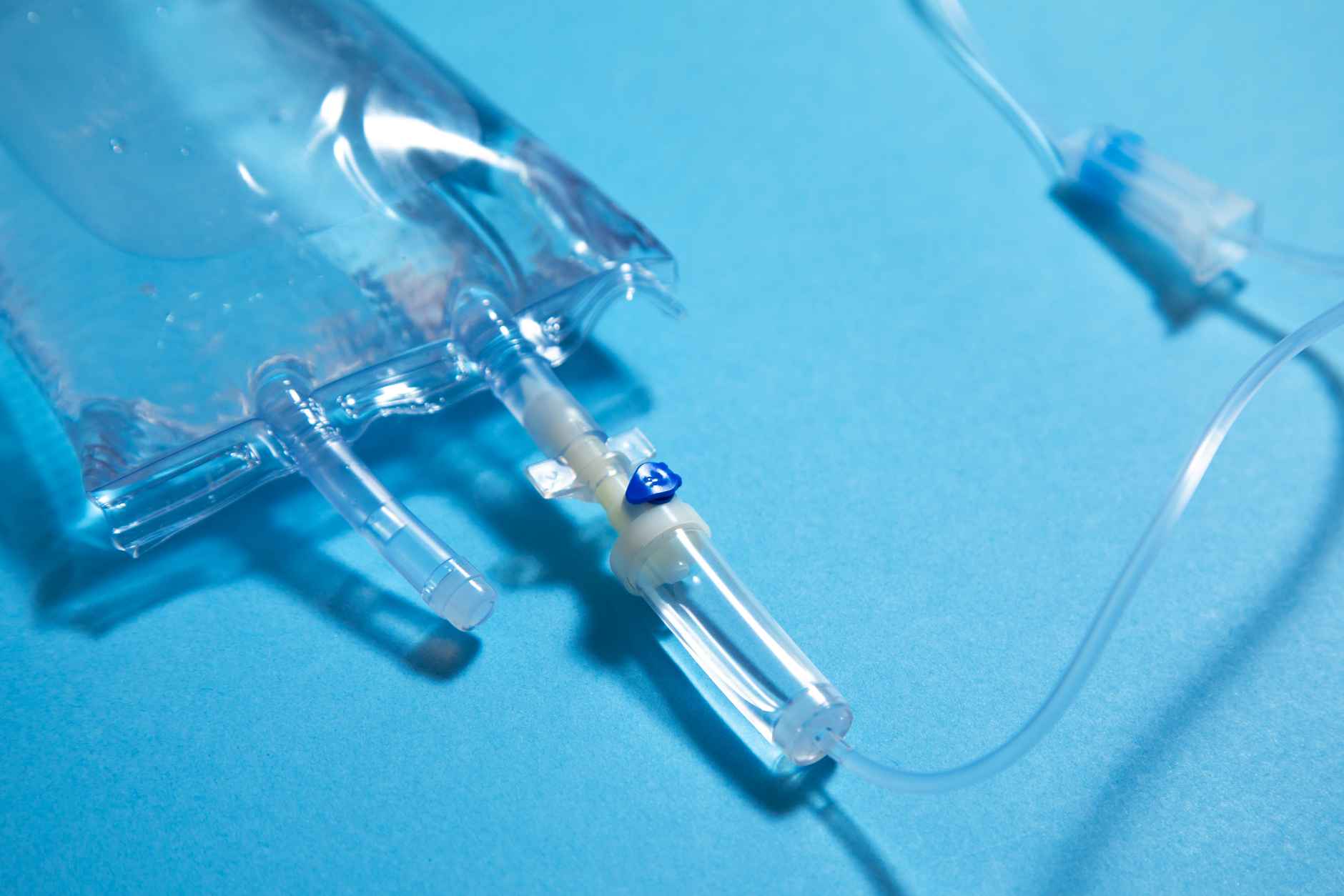
Table of Contents
- Introduction
- Key Applications of RF Sealing in Medical Welding
- The Benefits of RF in Medical Welding
- Partner With Vinyl Technology For Your Medical Welding and Device Manufacturing Needs
Radio frequency (RF) welding technology stands apart from traditional bonding techniques with its speed, precision, and inherent cleanliness. RF sealing is indispensable in medical welding and device manufacturing, where safety and reliability are paramount.
This medical welding process seamlessly merges compatible thermoplastic materials at the molecular level, producing bonds that offer extraordinary strength and leak-proof performance. In increasingly innovative medical devices, RF welding allows engineers and manufacturers to achieve designs and functionalities that would be difficult or impossible using other joining methods.
Key Applications of RF Sealing in Medical Welding
Radiofrequency (RF) capabilities are essential in medical welding and crafting devices. Here’s a closer look at how this technology directly benefits critical medical device categories:
Inflatable Medical Devices
Inflatable medical devices often play a direct role in patient care, making secure and airtight seals an absolute necessity. RF sealing is the ideal technology for ensuring the integrity of devices in medical welding. In blood pressure cuffs, strong welds maintain consistent pressure during readings, guaranteeing their accuracy.
Similarly, compression garments rely on these airtight seals to deliver targeted therapeutic pressure to specific areas of the body. During surgical procedures, tourniquets crafted in medical welding maintain a sterile field while managing blood flow. Across these applications, RF welding provides not only airtight seals but also ensures a smooth, comfortable surface for direct contact with patients, minimizing the risk of skin irritation.
The flexibility of RF sealing in medical welding extends beyond simple seals. Electrodes or dies designed with intricate or unique shapes can create various compartments and internal structures within inflatable devices. This ability enables manufacturers to produce sophisticated products tailored to specific medical needs.
Fluid Collection and Drainage
Medical devices designed for fluid collection and drainage demand absolute reliability to prevent leaks and contamination. RF welding excels in this area, creating exceptionally strong, hermetic seals that safeguard both patients and healthcare workers.
In blood collection bags, leak-proof seams formed by RF welding ensure that samples remain sterile and uncompromised for later analysis.
This technology applies equally to ostomy bags, providing dependable containment for patients and reducing the risk of infection. RF welded catheter drainage systems maintain secure connections, preventing accidental spills and safeguarding against the introduction of harmful bacteria.
Beyond simple strength, RF welding produces welds that are smooth and consistent, making them comfortable for patients. This factor is particularly critical in devices like ostomy bags, which may be in prolonged contact with sensitive skin.
Wound Care and Protection in Medical Welding
Wound care and the maintenance of sterile environments are cornerstones of effective medical practice, and RF welding plays a key role in these areas. Advanced wound dressings often incorporate multiple layers and materials expertly joined through RF welding.
This process allows for seamless transitions between absorbent layers, waterproof barriers, and breathable outer sections, offering superior protection and promoting healing. RF welding maintains material integrity even with complex or unusual dressing shapes.
Within operating rooms, RF welded surgical drapes establish well-defined sterile zones. These drapes provide physical barriers that help prevent the transmission of pathogens. During invasive procedures, RF welding is also used to create reliable protective covers for equipment and instrumentation, ensuring a pristine working environment.
As medical device needs evolve, the versatility of dielectric welding in medical welding enables even more innovative protective solutions in the years to come.
The Benefits of RF in Medical Welding
The applications of RF sealing in medical welding and crafting devices highlight clear advantages, but why is this technology so compelling for this demanding field? Let’s dive into the specific benefits that make RF welding a manufacturing cornerstone for medical products.
Medical Device Sterility and Cleanliness
In the world of manufacturing medical devices, sterility is non-negotiable. RF welding shines in this aspect, offering a joining method that’s inherently clean. As a non-contact process, it eliminates the need for adhesives, solvents, or additional materials that could introduce contaminants.
RF welding generates heat within the thermoplastic materials themselves, resulting in molecular-level bonds that form perfectly sealed barriers.
These hermetic seals effectively lock out any bacteria, viruses, or other impurities that could compromise a device’s effectiveness or put a patient at risk. This ability to provide absolute sterility underpins the widespread adoption of devices created in medical welding.
Device Reliability and Consistency
Medical devices must perform flawlessly without compromise. RF welding, when executed under controlled conditions, offers exceptional reliability and consistency. Modern RF welding equipment relies on precise control of power, frequency, time, and pressure.
Once optimal parameters are determined for a specific product, these settings can be exactly replicated time and time again.
This minimizes the potential for human error and ensures that every weld matches the desired strength and integrity. The result is a remarkably dependable manufacturing process that translates directly to safe and reliable medical devices.
Medical Welding Design Flexibility
RF welding unlocks new possibilities in medical device design. Unlike traditional joining methods that may impose limitations, RF welding works seamlessly with the inherent properties of thermoplastic materials. It’s possible to create welds in almost any desired shape or size by customizing the RF electrode to match the design.
Intricate contours, internal compartments, and complex geometries often required for specialized devices are achievable with this technology. RF welding facilitates the necessary functional structures within medical devices and creates smooth transitions and tapered sections to improve patient comfort and minimize potential irritants.
Partner With Vinyl Technology For Your Medical Welding Needs
Bringing a new medical device concept to market requires specialized knowledge and meticulous production processes.
At Vinyl Technology, we have extensive experience in applying RF welding technologies directly to manufacturing medical devices. Our engineers and manufacturing experts understand the complex needs of the healthcare industry, and we’re equipped to tackle the precise sealing demands of diverse medical devices.
We are committed to exceeding industry standards for product quality and process consistency. From design validation to full-scale production, we are ready to collaborate and translate your innovative ideas into functional medical devices.
If you’re seeking ways to improve reliability, expand your design possibilities, or streamline your medical device manufacturing, contact us today.
Let’s discuss how our expertise can propel your next medical device project forward.
Key Takeaways
- RF medical welding surpasses traditional joining methods in the demanding domain of medical device manufacturing due to its precision, speed, and cleanliness.
- This technology excels at creating leak-proof, hermetic seals – crucial for ensuring device safety, efficiency, and hygiene.
- RF welding empowers engineers to realize intricate device designs that may be infeasible with other bonding techniques.
Specific Applications
- Inflatable Devices: RF welding produces strong, airtight seams imperative for blood pressure cuffs, compression garments, and surgical tourniquets.
- Fluid Systems: Leak-free seals created by RF welding are foundational to blood collection bags, ostomy bags, and catheter drainage systems, preventing spills and contamination.
- Wound Care & Sterility: Medical welding enables advanced wound dressings with multiple layers and surgical drapes that safeguard sterile environments.
Compelling Benefits of RF Sealing
- Uncompromised Sterility: The process of RF welding is inherently clean, facilitating absolutely sterile devices and minimizing infection risks.
- Reliability & Consistency: Precise RF welding equipment provides highly repeatable results, assuring the performance and safety of each device in medical welding.
- Design Freedom: RF welding’s adaptability opens the door to intricate shapes and complex geometries within medical devices while providing smooth surfaces for patient comfort.
The Vinyl Technology Advantage
- The team at Vinyl Technology leverages extensive RF welding experience in the medical sector to fulfill complex product requirements.
- Commitment to high standards in quality and consistency fuels our manufacturing partnerships with healthcare innovators.