Understanding RF Welding Fabric and Material in Manufacturing
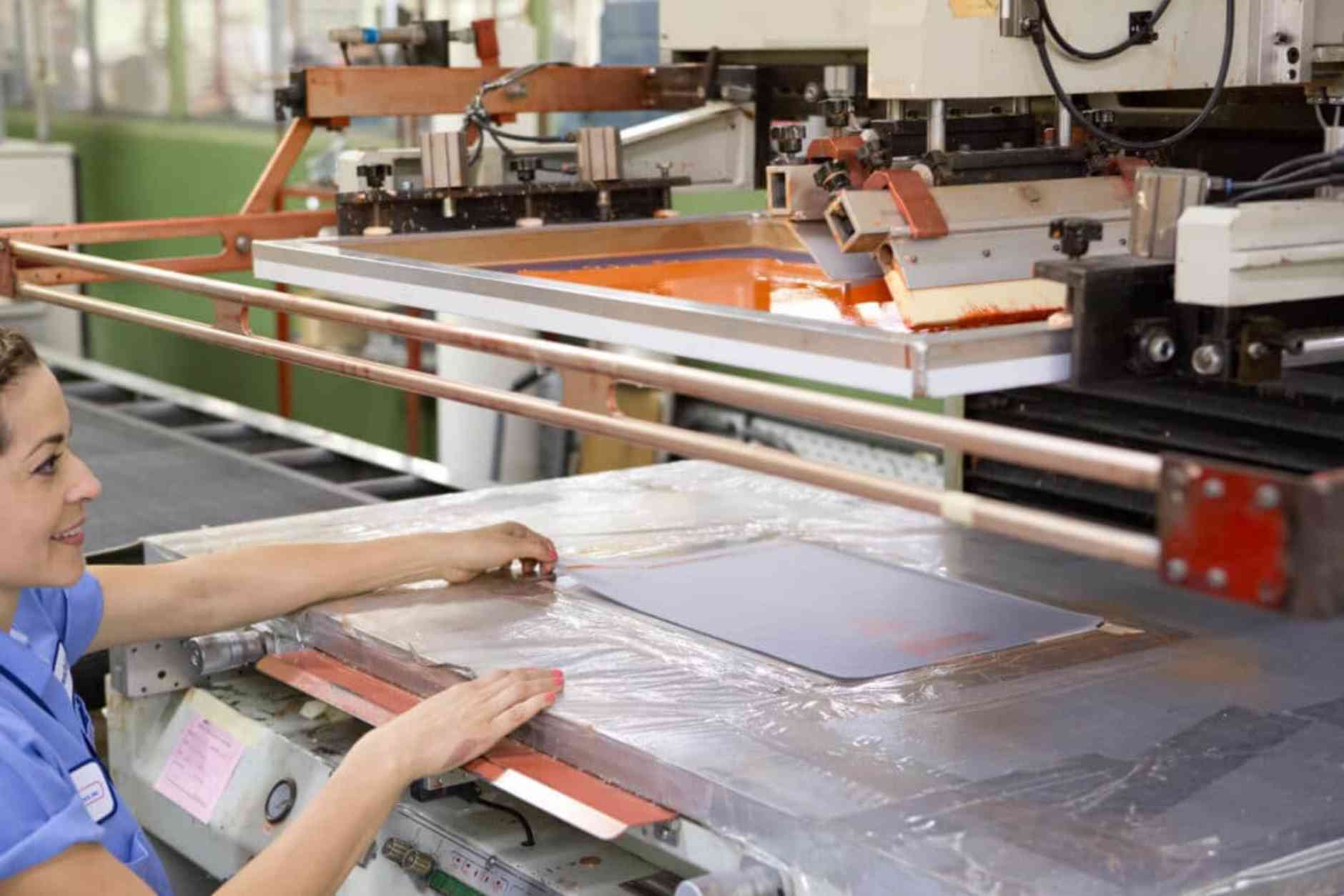
Table of Contents
- Introduction to Weldability in Industrial Manufacturing
- Fundamentals of the Right RF Welding Fabric
- Factors Influencing Weldability in Different RF Welding Fabrics
- Challenges and Solutions in Diverse RF Welding Fabrics and Materials
- Exploring Materials and Their Weldability in RF Welding
- Trust Vinyl Technology For Your Industrial Sewing Needs
- Key Takeaways
Weldability is a key concept in industrial manufacturing, especially in the field of RF (Radio Frequency) welding. It refers to the capacity of a material to be welded under specific conditions and still produce a strong, defect-free structure. The weldability of RF welding fabric is vital as it affects both the ease of welding and the quality of the finished product.
RF welding, a process that uses electromagnetic energy to fuse materials, heavily relies on the weldability of these materials. This method is prevalent in numerous industries due to its ability to create robust, airtight, and watertight seams.
The success of RF welding, especially in products like medical devices and automotive components, largely depends on the materials’ weldability.
Various RF welding fabric material properties, such as thermal conductivity, melting point, and chemical composition, impact this. Each material reacts differently to the RF welding process, and this reaction is crucial in determining the overall efficiency and outcome of the manufacturing process. For example, materials with similar thermal properties and melting points tend to produce more effective welds.
In sectors like industrial sewing and manufacturing, where RF welding is integral, selecting the right material based on its weldability is essential. This selection is critical for ensuring the longevity of products like safety gear and the reliability of inflatable structures. Understanding weldability is, therefore, not just about RF welding fabric material selection; it’s about enhancing the manufacturing process and ensuring the production of high-quality, reliable products, which is fundamental for industry success.
Fundamentals of the Right RF Welding Fabric
The right fabric for RF welding involves the capacity of materials to form a bond under the influence of radio frequency energy. This bonding process is critical in many manufacturing applications, from medical devices to automotive interiors.
RF welding works by applying electromagnetic energy to the materials to be joined, causing them to heat and fuse together. This process is unique because it doesn’t require external heat or adhesives. Instead, the energy directly interacts with the RF welding fabric, making the welding precise and clean.
The effectiveness of this process depends largely on the material’s ability to absorb and respond to the RF energy.
Different materials have varying RF responsiveness levels, directly impacting their weldability. Materials with high dielectric loss factors are generally more responsive to RF energy and weld more effectively. This responsiveness is crucial as it dictates the strength and durability of the weld.
Materials with poor RF responsiveness may not weld efficiently, leading to weak joints that could compromise the integrity of the final product.
The weldability of certain RF welding fabrics is also affected by their thickness and composition. Uniformity in material thickness ensures consistent heating and welding, while variations can lead to uneven welds. The chemical composition of materials also plays a significant role, as certain additives or impurities can enhance or hinder the welding process.
Understanding these fundamental weldability aspects allows manufacturers to make informed decisions about RF welding fabric selection and process parameters. This knowledge keeps the welding process efficient and produces products that meet the high standards of strength, safety, and durability required in many industrial applications.
Factors Influencing Weldability in Different RF Welding Fabrics
In RF welding, the choice of material is critical, and several factors influence the weldability of different materials. Understanding these factors is key to a successful and efficient welding process.
- Thermal Conductivity: Materials with high thermal conductivity dissipate heat quickly, which can be challenging in RF welding as it may lead to uneven or weak welds. Conversely, RF welding fabrics with lower thermal conductivity retain heat better, allowing for stronger, more consistent welds.
- Melting Point: The melting point of a material is crucial in RF welding. Materials with a lower melting point are generally easier to weld as they require less energy to fuse. However, materials with very low melting points can be prone to distortion during the welding process.
- Chemical Composition: The chemical makeup of RF welding fabric can significantly affect its weldability. Certain chemicals or additives within the material can either enhance or interfere with the RF welding process. For instance, some additives can increase a material’s sensitivity to RF energy, improving weldability.
- Thickness and Uniformity: The thickness of the welded materials plays a significant role in the welding process. Thicker materials may require more energy to weld effectively. Uniform thickness across the welding area is also important for consistent energy absorption and welding strength.
- Surface Properties: The surface properties of the RF welding fabri, such as roughness or coatings, can impact the process. Smooth, clean surfaces generally weld better as they allow for better energy transfer and less interference during the welding process.
- Compatibility of Materials: When welding different materials together, their compatibility is crucial. Materials with similar properties, such as thermal conductivity and melting point, tend to weld better together, leading to stronger bonds.
By carefully considering these factors, manufacturers can choose the most suitable RF welding fabric. This careful selection contributes to the final product’s quality and durability.
Challenges and Solutions in Diverse RF Welding Fabrics and Materials
Welding diverse materials in RF welding involves navigating a range of challenges, each requiring specific solutions to ensure high-quality outcomes.
Inconsistent material properties are a common hurdle, as different materials can react variably to RF energy. This can lead to welds that are not uniform in strength or appearance.
To overcome this, manufacturers often conduct pre-tests on RF welding fabrics to understand how they will respond to the process. These insights allow them to fine-tune the welding parameters, such as power levels and exposure time, to achieve consistent results.
Another challenge arises from variations in material thickness. Materials of uneven thickness can result in uneven welding, where some parts may be over or under-welded. Addressing this issue typically involves selecting RF welding fabric with uniform thickness.
Alternatively, adjusting the welding process to account for these variations can lead to more uniform welds.
The sensitivity of certain materials to high temperatures is another concern. When exposed to high heat, materials prone to degradation or distortion require a delicate approach. Lowering the power settings and reducing the welding cycle duration are effective ways to prevent material damage while achieving strong welds.
Surface contaminants such as dust, oil, or moisture can impede welding. These contaminants can create barriers that interfere with the energy transfer necessary for effective welding.
The solution lies in ensuring that RF welding fabrics are clean and dry before they undergo the welding process. This simple but crucial step can significantly enhance the quality of the welds.
Compatibility issues between different types of materials present yet another challenge. Materials with differing melting points and thermal properties can be difficult to weld together effectively. In such cases, choosing materials with similar characteristics or using intermediate layers that bond well with both materials can be effective strategies.
The limitations of welding equipment can sometimes restrict the process, especially when dealing with complex shapes or designs. Customizing the equipment or creating specialized fixtures to accommodate these unique product requirements can greatly enhance the welding process’s efficiency and effectiveness.
By addressing these challenges with thoughtful and tailored solutions, manufacturers can successfully weld various materials for the final products that meet the highest quality and durability standards.
Exploring Materials and Their Weldability in RF Welding
The selection of RF welding fabrics and materials is pivotal for achieving optimal results. Different materials exhibit varying degrees of weldability based on their inherent properties. Here’s a look at some common materials used in RF welding and insights into their weldability:
- Polyvinyl Chloride (PVC): PVC is known for its excellent weldability in RF welding. It responds well to RF energy, allowing for strong, consistent welds. Its versatility makes it a popular choice for a wide range of products, including waterproof items.
- Polyurethane: Polyurethane exhibits good weldability, particularly in applications requiring flexibility and durability. It is often used in medical devices and inflatable products due to its strong bonding capabilities.
- Polyethylene: While polyethylene can be welded using RF welding, it presents some challenges due to its lower dielectric loss factor. It requires careful control of welding parameters to achieve effective results.
- Nylon: Nylon, especially certain types, can be more challenging to weld using RF energy. This RF welding fabric often requires specific conditions or additives to enhance its weldability and is typically used in applications where its other properties, like abrasion resistance, are desired.
- Polypropylene: Polypropylene is generally considered to have fair weldability in RF welding. It requires precise control over the welding process but can be effectively used in various applications once these parameters are optimized.
- Teflon (PTFE): Teflon is known for its poor response to RF welding. This RF welding fabric’s inherent properties make it resistant to the process, often requiring alternative methods for effective bonding.
Understanding these properties is crucial for manufacturers to select the right material for their specific welding needs for both the efficacy of the process and the quality of the finished product.
Trust Vinyl Technology For Your Industrial Sewing Needs
The art of RF welding is a nuanced process, deeply influenced by the choice and properties of materials used. By carefully selecting RF welding fabrics and materials and tailoring the process to their specific properties, manufacturers can ensure that their products are well-crafted but also durable and reliable.
For businesses and organizations looking to leverage the benefits of RF welding in their products, partnering with an experienced manufacturer is crucial.
This is where Vinyl Technology comes into play. With our extensive experience in RF welding and custom industrial sewing, we specialize in transforming challenging materials into high-quality products.
Whether you need RF welding fabrics, medical devices, or any other product that requires the precision and durability of RF welding, our team at Vinyl Technology is equipped to deliver. Our commitment to quality, safety, and efficiency ensures that your products are not just made, but masterfully crafted to meet the highest standards.
Key Takeaways
- Understanding Pricing: Grasping the various components of pricing, such as material and labor costs, is essential for making informed decisions and negotiating effectively.
- Material Costs: The choice of RF welding fabric, threads, and accessories can significantly impact the overall cost and quality of the final product.
- Labor Costs: Balancing the skill level required for your project is crucial for optimizing costs. Skilled labor comes at a premium but ensures high-quality output.
- Overhead Costs: Utilities and workspace rent are often overlooked but are integral to the pricing structure.
- Industry Variances: Regional and seasonal factors can influence labor rates and material costs, affecting the overall project cost.
- Negotiation Strategies: Research, clear communication, and price comparison are key tactics for effective negotiation with service providers.
- Market Trends: Being aware of seasonal and economic trends can help you plan your projects more effectively and provide additional negotiating leverage.
- Volume Discounts: Leveraging bulk orders and long-term contracts can result in substantial cost savings.
- Vinyl Technology: A trusted partner for businesses seeking custom RF welding, RF sealing, and industrial sewing services focused on quality and efficiency.